Plastic injection moulding is one of the most widely used processes in manufacturing today. From automotive components to consumer electronics and medical devices, the technique allows for mass production of complex plastic parts with speed and accuracy. At the heart of this process is a critical component—the injection screw. For businesses in Southeast Asia, choosing the right plastic injection screw Malaysia provider can have a major impact on production quality and efficiency.
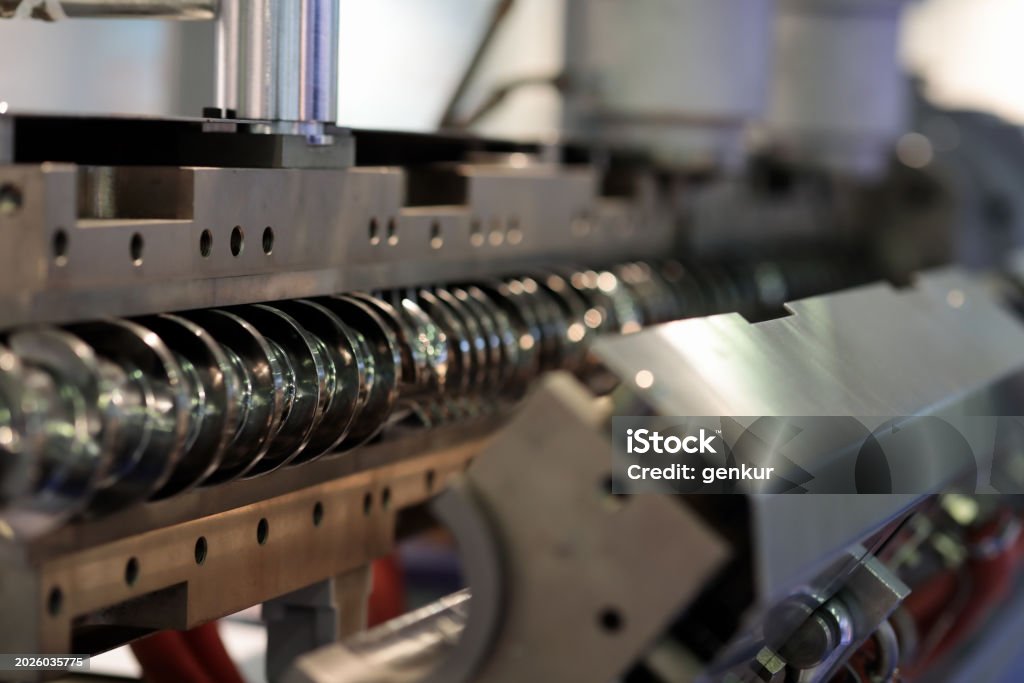
The injection screw is responsible for melting, mixing, and pushing plastic material into a mould. While it may sound simple, its design and material composition are key factors that influence consistency, cycle time, and even energy consumption. A well-engineered screw ensures better melt homogeneity, which leads to fewer defects and higher part quality.
Some of the key benefits of using the right screw configuration include:
- Improved melt flow and temperature control
- Reduced energy usage and cycle time
- Better mixing of additives and colourants
- Longer equipment life due to less wear and tear
With increasing pressure on manufacturers to improve output while reducing waste, precision components like injection screws are now more important than ever. Whether you’re producing thin-wall packaging or structural parts, working with a trusted plastic injection screw Malaysia supplier ensures your production line runs smoothly.
Modern injection screws can be tailored to different types of polymers, including high-performance engineering plastics, biodegradable resins, and recycled materials. Factors such as screw length-to-diameter ratio, compression zones, and mixing sections must be optimised based on the application. That’s why technical consultation and after-sales support are important considerations when selecting a supplier.
Many manufacturers also seek providers that offer related equipment and support systems—such as barrels, nozzles, and extrusion components. This integrated approach can simplify maintenance, reduce downtime, and ensure greater compatibility across machinery.
In Malaysia, several suppliers have expanded their capabilities to meet the needs of today’s high-demand production environments. They offer custom solutions for various industries, including automotive, consumer goods, electronics, and packaging. A reliable resource for exploring these solutions can be found here, where a wide range of injection and extrusion support materials is available.
Choosing the right plastic injection screw Malaysia partner isn’t just about sourcing a component—it’s about ensuring consistent, high-quality output. With tighter tolerances and faster turnaround expectations, manufacturers need every element of their process to work efficiently.
By investing in better tooling and materials, businesses not only improve product quality but also gain a competitive edge in a crowded market.